Aviation
With customer service as a priority in mind, we are obligated to work on lowering costs and raising the capabilities across the aerospace and defense industry. In this regard, Nordisch offers simulation software to assess the current performance and determine the remaining service life (URL) of cables, rubbers, O-rings, adhesives, and polymer composite structures used in the aircraft.
From all parts of the aerospace and defense industry, we are promised to level up the customer’s expectations by crossing the bridge between virtual and hands-on operations. The efficient and safe passage of electrical and power signals between the electrical components of the aircraft is essential for the continued safe functioning of the aircraft after its planned lifespan. This calls for maintaining the physical characteristics of electrical cables and wires as well as their insulation. The wire insulation may deteriorate to the point that it can no longer guarantee the safe transfer of electrical current as an aircraft gets older and through more cycles. Our team at Nordisch investigated the causes of wire insulation degradation and tested the methods to predict when a wire would lose its ability to conduct electrical current.
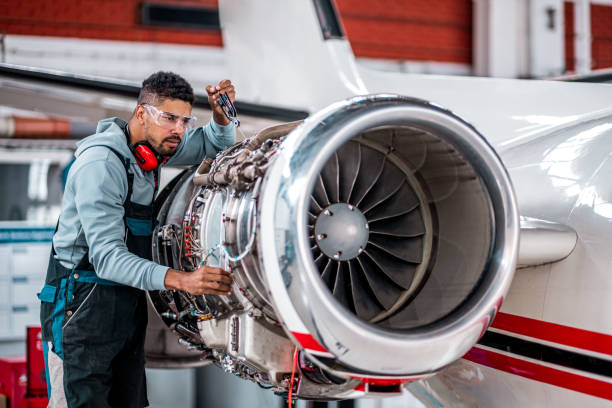
Dynamic bending, thermal cycling, vibration, chemical exposure, electrical stress, static stress, temperature, humidity, and airflow are a few of the multivariable factors that can influence the age of aircraft wires and cables. Other factors include thermal oxidation, chemical oxidation, photo-oxidation, ultraviolet exposure, and hydrolysis. A worn-out wire is more vulnerable to these forces than a new one, and the chance of the insulation failing rises with time.
Very basic, method for realizing that a wire/cable is aged or needs to be replaced is monitoring it, which is a long-time, costly, and incorrect process. The main problem is unknown time of replacing the cable/wire, which will increase the potential of any unexpected failure. One of the unexpensive way to solve this problem for aircraft’s wire is using predictive tools to prediction wire lifetime.
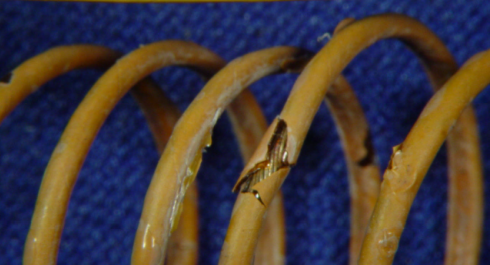
Besides developing a multi-physics simulation tool for polymers, Nordisch developed a similar Multiphysics tool (NordPoly) that helps our customers quickly assess the residual structural integrity of thermoset polymer composite aircraft structures subjected to excessive heat. This addresses the need for Naval aircraft in operation that faces the risk of over-temperature incidents such as fires and high-temperature exhaust gas impingement. By using NordPoly our customer can protect the composite aircraft structures from excessive heat since thermally damaged composites are vulnerable to compressive failure in the aircraft structure.